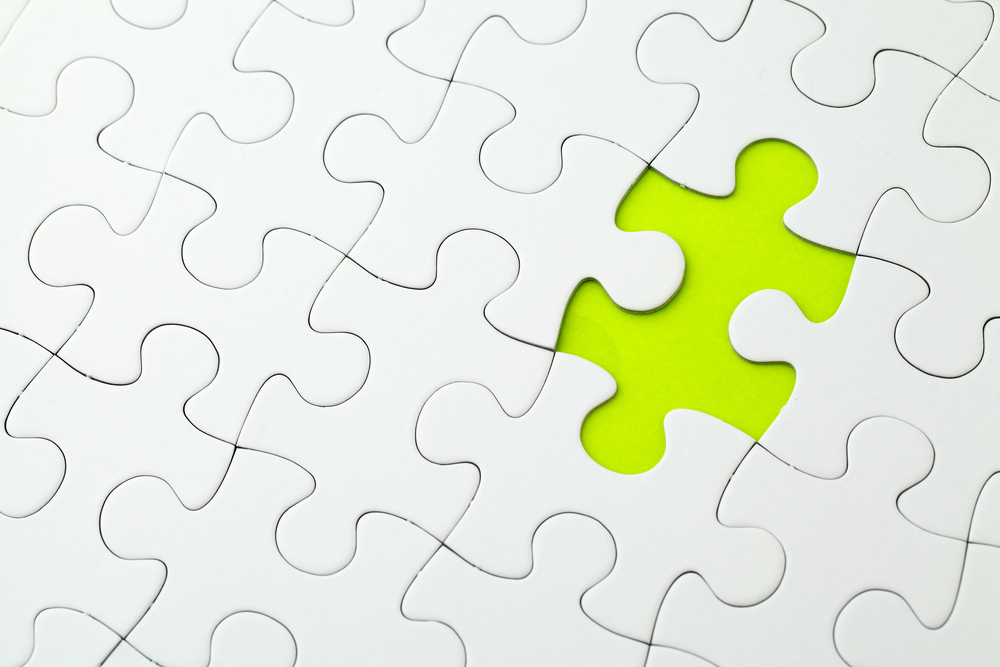
Project & Product Criteria
The criteria that will shape every new lighting project to ensure the best results are achieved.
What Will You Learn About Project & Product Criteria?
We discuss two factors that customers must consider when taking on any LED lighting project:
Project criteria
Product criteria
Why does this matter?
- Without considering these factors and their many facets, you're leaving yourself vulnerable to faulty LED products and the inevitable faulty lighting performance!
We're helping you learn what matters in the world of LED lighting.
What do we mean by “Project Criteria?”
Project criteria is the framework or outline customers set based on what they want to achieve with their lighting project. At Stouch Lighting, we often refer to this as a customer’s “desired outcome.” You choose your project criteria based on this desired outcome.
The project criteria is set by the customer, NOT the lighting supplier or manufacturer, and often consists of the below criteria. We go into detail on each below.
You can click these terms to jump directly to each corresponding explanation!
- Light levels
- Warranty length
- Budget
- Product lifetime
- Implementation timeline
- Implementation restrictions
- Lighting applications
- Return on investment requirements
- Lighting outcome priorities
What do we mean by “Product Criteria?”
The product criteria are the technical specification and performance attributes of individual LED fixtures and lamps. This information is generated from industry-approved testing methods, processes, and laboratories. It's imperative that you derive the product criteria from these industry-approved testing methods only so you don't end up with lighting that does not meet its expected performance standards.
Click here to jump to Product Criteria, Explained.
Project Criteria, Explained
As mentioned, project criteria is the framework customers set based on what they want to achieve with their lighting project. Below are project criteria that you may select and define when outlining your lighting project plan.
Light Levels
Light levels, measured in foot-candles, are essentially the amount of light reaching a given surface. A customer should ask a supplier to provide a photometric layout to prove that the products they are proposing will meet the light levels required for the customer, space, building, etc. If they can’t provide the photometrics, that’s a red-flag that either the vendor or the manufacturer in consideration is offering substandard products, since any product that has gone through the necessary industry standard testing will have the reports to generate photometric layouts.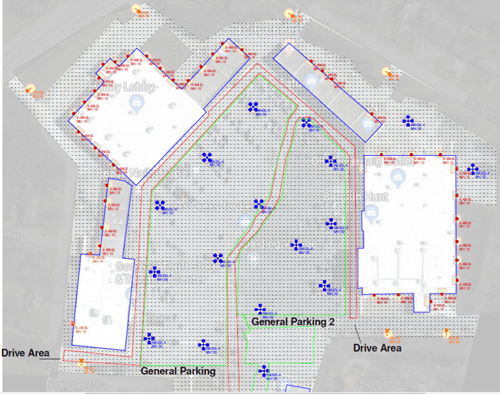
Warranty Length
How long of a manufacturer warranty do you want? The emphasis is on MANUFACTURER, as you want the product to be supported by the company that made it. Often, a supplier or vendor will add a few years on top of the manufacturer’s warranty on their own, saying things like, “well, the product warranty is five years but we will give you an additional five years on top of that.” What does that really mean? It means they are offering you a product that does not meet an aspect of your carefully selected project criteria and trying to make up for it with their "additional warranty." If a manufacturer warranties a product for five years, that’s how long they plan on supporting that particular product or model. What happens in year seven when there is an issue with the product? Is the vendor you used seven years ago going to replace that fixture with a product from the same manufacturer? What if the manufacturer no longer provides components or supports that particular model? Is that vendor going to buy you a completely new or different fixture, maybe from a different manufacturer? Good luck keeping track of your product warranties after that.
Manufacturer warranties should be listed on the product cut sheets/specification sheets or provided as a statement on their letterhead and signed by someone with the authority to do so. If a turnkey vendor provides a product cut sheet with their own branding on it (not showing who actually manufacturers the product), make sure you find out who actually MAKES the fixture (since it’s very unlikely your turnkey lighting vendor manufacturers, distributes, and installs LED lighting fixtures) and obtain a cut sheet from that manufacturer so you can see the true product information.
Budget
This one is straightforward. How much money do you have to spend on a project? Many customers hesitate to provide potential vendors with a budget out of fear that those vendors will price out their solutions to maximize your budget, which is an understandable concern. Don’t forget, however, that LED lighting is not a commodity and it is important to understand that simply seeking the cheapest material without establishing your project and product criteria (keep reading, we'll get to product criteria) properly will leave you with exactly that, the cheapest material. When it comes to LED lighting the phrase, “you get what you pay for” is unfortunately very accurate. It’s not like lighting is a minor aspect of your businesses. You need it so your customers can safely drive and park their cars, or clearly see the merchandise you’re selling. Think of it this way; sure, you can buy a car for $500, but are you going to rely on that car to get to work every day?
Product Lifetime (L70 rating)
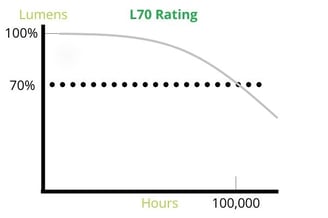
LED product lifetimes are measured in hours and often include the term “L70." L70 is the point in time (measured in hours of operation) when the initial light output of a lamp or fixture has degraded by 30%. Not all LED products have the same lifetime, and that’s okay. For example, the L70 of an LED fluorescent tube replacement is much different than that of an LED parking lot fixture, but that doesn’t mean the LED tube is low quality. You will need to establish the rated lifetime criteria for each of the products and applications in your project. For example, minimum L70s of 50,000 hours for LED T8 lamps, 100,000 hours for LED high bay fixtures, 125,000 hours for LED parking lot fixtures, etc. A manufacturer-neutral supplier or vendor should be able to provide guidance on what lifetime standards a customer should expect. The most important part about product lifetimes is that they are not simply something a manufacturer arbitrarily claims. L70 claims are generated from independent testing results (more on that later). So just because a product cut sheet says L70 = 100,000 hours, unless the manufacturer can provide the supporting documentation to prove it, it’s just a number on a piece of paper. And to make it extra confusing, L70s should be based on TM-21.
Implementation Timeline
When do you plan to start and when do you need to be done? The reason this is important is that not all manufacturers have domestic inventory. In fact, many products are built-to-order or must be shipped in from foreign countries such as Korea and China. This can mean a very long lead time. The reality of the LED lighting industry is that there are a lot of products that look great on paper and have all of the required technical specifications and testing results to support their product performance claims, but if they can’t produce and deliver the volume your project requires within the time constraints you require, those products aren’t valid options. Being able to deliver material in the time frame needed is a key component of your project criteria. Be sure to require that any vendor you are considering can prove that they can deliver the material on time.
Implementation Restrictions
When can the installation or deliveries occur? Different customers have different restrictions on when lighting projects can be implemented. For example, retail companies may require that any interior lighting project be completed before or after regular 9-5 business hours to avoid interfering with their day-to-day business. Whereas a shopping center may need its parking lot lighting converted to LED during the day. The reason this is important is because installation and deliveries that occur before or after your typical 9-5 business hours can result in higher labor rates and limit the ability to scale implementation on locations with multi-site projects, which can affect your budget and implementation timeline. Forgetting to specify implementation restrictions in your RFP or bid documents can result in receiving pricing from vendors that does not accurately reflect the true cost of your project.Lighting Applications
What types of lighting are you looking to purchase or convert to LED? By “application” we mean products such as parking lot, wall pack, garage and canopy, high mast, sports field, fluorescent replacements, troffers, high bays, vapor tights, etc. Basically, what applications of your interior or exterior lighting do you want to address/change? The reason customers need to clarify what LED lighting applications they want to purchase is because, as we mentioned, different LED applications have different lifetime standards, warranties, and other product criteria, and having an understanding of your intended lighting upgrade enables you to get the technical specifications you desire. For example, if you are replacing the fluorescent lighting in the interior for your building or facility and the parking lot lighting in the exterior, you need separate sets of product criteria for each application. If you were to use an LED T8 L70 of 50,000 hours for both the fluorescent replacements and parking lot lighting, you would get a quality LED T8 lamp, but drastically sell yourself short on the exterior lighting, since its L70 should be a minimum of 100,000 hours.
Return on Investment (ROI) Requirements
This project criterion applies mostly to retrofit and conversion projects and not so much to new construction projects (since the project’s budget usually addresses potential product pricing).
Speaking of budget, that is NOT what we mean here. What we are talking about are return on investment (ROI) requirements. Is there an ROI requirement for your project? Do you need to see a payback in five years? Three years? Your vendor understanding the investment criteria is helpful because it helps to narrow down the viable LED product solutions. If your vendor understands your operating conditions, such as energy cost (kWh rate), hours of operation, maintenance expenses, etc., they should be able to select LED products with the appropriate price points and technical characteristics to ensure that the required ROI is achieved. Setting the ROI also ensures that all stakeholders are on the same page regarding expectations during the RFP or bid development process. For example, if you have a warehouse that currently utilizes four lamp fluorescent T5 fixtures, operating six hours a day, five days a week, paying $0.04 per Kwh, all while using occupancy sensors, and you are requiring an ROI of two years for a lighting conversion to LED, your vendor should probably tell you up front that it is unlikely that you are going to achieve that ROI.
Lighting Outcome Priorities- Of Particular Importance!
- This aspect also applies mostly to retrofit and conversion projects, not so much to new construction projects
- By project lighting criteria we mean— what are the primary issues you are trying to address? Every lighting project affects customers in three primary ways:
- Energy consumption
- Maintenance costs
- Lighting performance
.
.png?width=442&name=Copy%20of%20Copy%20of%20Untitled%20(6).png)
- Example One
-
- Let’s say you are a national convenience store retail chain, and one of your biggest issues with your lighting is that every time one of your parking lot lights goes out you must call an electrician to bring out a bucket truck or lift to fix your lights. You must react to these outages quickly because if your exterior lights are out, customers will just drive right by thinking that your store is closed, or worse, because they wouldn’t feel safe parking in a dark lot. This reactive method of fixing your lights is very expensive since rolling out bucket trucks and lifts is not cheap. In this scenario your order of priority is:
- Maintenance cost reduction
- Lighting performance improvement
- Energy consumption reduction
- Let’s say you are a national convenience store retail chain, and one of your biggest issues with your lighting is that every time one of your parking lot lights goes out you must call an electrician to bring out a bucket truck or lift to fix your lights. You must react to these outages quickly because if your exterior lights are out, customers will just drive right by thinking that your store is closed, or worse, because they wouldn’t feel safe parking in a dark lot. This reactive method of fixing your lights is very expensive since rolling out bucket trucks and lifts is not cheap. In this scenario your order of priority is:
-
- Knowing this order of priorities allows your vendor to narrow down the LED lighting solutions to consider. Since maintenance costs are the primary pain point, products with a longer and more comprehensive warranty are the focus. Meaning you would only consider products with a manufacturer warranty of, say, 7-10 years, thus eliminating from consideration any product with only a five year warranty. Once that filter has been applied you then narrow down further the options to consider by having the vendor or manufacturer complete photometric layouts (remember those?) to ensure that you are getting the light levels (foot-candles) you require for your site. The energy savings that you realize from this conversion is the pepperoni or icing on top (back to the pizza/pie reference).
- Example Two
-
- Get it yet? No? Okay, let’s try another one. Let’s say you are a facility manager responsible for a large distribution center that operates 24 hours a day, 7 days a week. The lighting in your facility (consisting primarily of high bay fixtures) is the second biggest consumer of energy in the facility, after heating and cooling. Your existing light levels are fine, but you could probably do without the interference of breaking out a lift and shutting down an aisle to repair fixtures every time one goes out (the facility is operating 24/7 after all). In this scenario your priorities are:
- Energy consumption reduction
- Maintenance cost reduction
- Lighting performance improvement
- Get it yet? No? Okay, let’s try another one. Let’s say you are a facility manager responsible for a large distribution center that operates 24 hours a day, 7 days a week. The lighting in your facility (consisting primarily of high bay fixtures) is the second biggest consumer of energy in the facility, after heating and cooling. Your existing light levels are fine, but you could probably do without the interference of breaking out a lift and shutting down an aisle to repair fixtures every time one goes out (the facility is operating 24/7 after all). In this scenario your priorities are:
-
- Knowing these priorities, your lighting vendor should focus on LED fixtures with a high efficacy, meaning high lumens per watt. Basically more “efficient” fixtures. By focusing on this characteristic, the customer is getting the most “bang for their buck” in regard to the light levels achieved (we are assuming your vendor and manufacturer provided a photometric layout of any products in consideration to ensure the conversion to LED would not result in a degradation of foot-candles). Your new vendor should then consider implementing lighting controls. Are there certain areas of the building that are occupied less than others? Could occupancy sensors and dimming be implemented? Adding controls in a facility with high hours of operation can add significantly to the energy savings already realized from the conversion to LED.
Our Service Offering
Product Criteria, Explained
As we mentioned earlier, product criteria (NOT PROJECT CRITERIA) are the technical specification and performance attributes of individual fixtures and lamps. This information is generated from industry-approved testing methods and processes. The manufacturer of any LED product in consideration for a project of ANY size needs to be able to provide validation that the technical specifications listed are accurate. We cannot stress this enough!
Technical Specifications Relevant to all Lighting
Below is a list of some technical specifications that should be listed on a manufacturer’s product cut sheet.
- Wattage
- Color rendering index (CRI)
- The ability of the light generated from a lamp or fixture to render the color of the object that is being illuminated accurately
- CRI definition
- Correlated color temperature (CCT)
- The color of the light that is generated
- CCT definition
- Color stability
- The range of color shift (CS) that a manufacturer states may occur within a lamp or fixture’s warranty period
- Color stability definition
- Color uniformity
- Range of color difference (CCT) of individual diodes within a lamp or fixture
- Color uniformity definition
- Lumen output
- Total light generated from lamp or fixture, measured in “lumens”
- Generated from LM-79
- Lumen output definition
- Efficacy
- Lumens per watt
- Generated from LM-79
- Efficacy definition
- Lifespan/rate life/L70
- Rated life of LED lamp or fixture
- Generated from LM-80 and TM-21
- LM-80 definition
- TM-21 definition
- Operating voltage
- What voltage the LED driver within a lamp or fixtures requires
- UL listing (or equivalent)
- LM-79, LM-80, TM-21 testing and results
- Ambient temperature range
- Range of ambient temperatures in which the lamp or fixture can operate
- Housing material
- Material with which a lamp or fixture is constructed
- Mounting
- What type of pin or socket does a lamp utilize? How is a fixture hung from a ceiling or mounted to a pole, etc.?
- Ingress projection rating (IP)
- A fixture’s ability to withstand dust and water intrusion
- IP definition
- Total harmonic distortion
- Measurement of the harmonic distortion present in a signal; defined as the ratio of the sum of the powers of all harmonic components to the power of the fundamental frequency. This will relate to the power supplies only and they are the only component that generates any kind of frequency.
- Total harmonic distortion definition
- Another total harmonic distribution definition
- New lamp effect definition
- Power factor
- Power factors derived from dividing “real power” by “apparent power.”
- Power factor definition
- Warranty
- A time period in which a manufacturer guarantees (under specifically listed conditions) that a lamp or fixture will operate. Be sure to check what the manufacturer means by “operate,” and how they will back up that “guarantee.”
- Surge protection
- The level to which an LED fixture or lamp can withstand a transient electrical surge
- Surge protection definition
- Weight
- The weight of the fixture or lamp
- DLC or Energy Star Listing
- Intendant certifying bodies of manufacturer testing results. Most utility companies that provide rebates for LED lighting require a product to be listed on either the Design lights Consortium Qualified Product or on Energy Star. These listings are NOT a confirmation of quality, just a set of basic testing criteria required.
Technical Specifications Relevant to Outdoor Lighting
- Effective project area (EPA)
- Measurement of a light fixture, pole, mounting bracket, etc., drag profile. A wind rating that provides guidance on a structure’s ability to withstand various wind speeds.
- EPA definition
- Mounting
- The mounting method of an LED fixture or lamp
- IES distribution pattern
- Projected pattern of light of a fixture onto a surface
- IES distribution pattern definition
- BUG rating
- Measurement of a fixture's backlight, uplight, and glare
- BUG rating definition
Technical Specifications Relevant to Unique or Hazardous Location Environments
- NSF
- Certification that a fixture is constructed for use in controlled environments such as pharmaceutical processing, biotech research, biosafety laboratories, surgical suites, clean room manufacturing, food processing, and horticulture
- NSF definition
- NEMA
- Certification of a fixture’s ability to withstand certain environmental conditions
- More on NEMA
- Even more on NEMA
- UL844 listing
- UL listing for LED luminaires for use in hazardous classified locations
- UL844 definition
- ISO
- Cleanroom classification
- ISO definition